Marnotrawstwo czasu w organizacji – analiza wyników badań
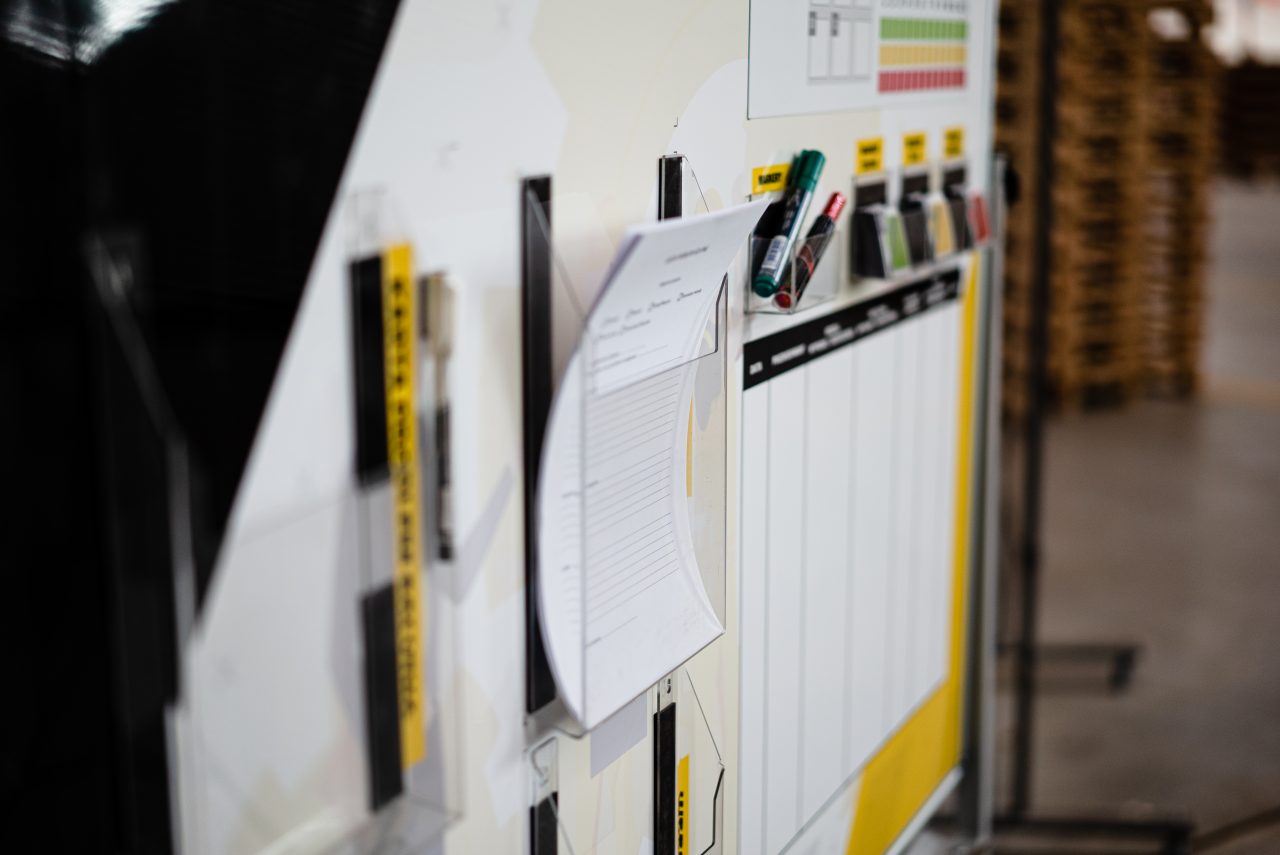
24% – tyle czasu średnio tracą pracownicy średniego szczebla w firmach produkcyjnych na proste czynności, związane z raportowaniem, poszukiwaniem dokumentacji czy przekazywaniem zmiany. Tak wynika z raportu opublikowanego przez KanriSoft. Podobnie kształtują się wyniki dla pracowników produkcji. Czy marnotrawstwo czasu jest czymś wpisanym w specyfikę działania firm? A może jednak da się mu zapobiegać?
Poszukiwany – poszukiwana
Na co tracą czas kierownicy średniego szczebla? Na poszukiwania:
- Poszukiwanie dokumentacji stanowiskowej zabiera średnio 11 minut podczas ośmiogodzinnej zmiany
- Poszukiwanie historycznych danych: średnio kolejne 18 minut.
Łącznie to blisko pół godziny szukania. Problem nie dotyczy jednak tylko kierowników – przeciętny pracownik produkcji spędza 16 minut dziennie na… poszukiwaniu przełożonego!
Obraz wydaje się paradoksalny – przełożony szuka dokumentacji, pracownik w tym samym czasie szuka przełożonego… a to jedynie wierzchołek góry lodowej.
Przekazywanie i oczekiwanie
Najwięcej czasu kierownicy tracą na przekazywanie zmiany. Z kolei pracownicy produkcyjni – na oczekiwanie na komponenty. Obydwa procesy zajmują średnio po 38 minut w trakcie zmiany.
To znaczy, że pracownik produkcji na oczekiwanie na komponenty i poszukiwanie przełożonego traci przeciętnie 54 minuty dziennie. To ponad 11% jego zmiany!
Kierownik, na poszukiwania dokumentacji, danych historycznych i przekazywanie zmiany poświęca aż 14% swojego czasu. Ale… to wciąż nie wszystko.
Liczenie
Kolejną czynnością, która zajmuje czas kierownika, jest liczenie:
- kalkulacja wskaźnika OEE: średnio 33 minuty
- liczenie wyprodukowanych sztuk: średnio 10 minut
Łącznie: 43 minuty, czyli kolejne 9% zmiany.
Pracownicy produkcji nie marnotrawią czasu na liczenie – za to marnują go na zdarzenia związane z nieprawidłowym funkcjonowaniem:
- zgłaszanie awarii: średnio 8 minut
- zgłaszanie przyczyn przestoju: średnio 9 minut
- raportowanie bezpieczeństwa: średnio 6 minut
- zgłaszanie i kategoryzacja błędów: średnio 12 minut
Łącznie: kolejne 35 minut. Kolejne 7% zmiany.
Przyczyny
Łącznie na wymienione czynności (oraz inne podobne) pracownicy średniego szczebla poświęcają przeciętnie 117, a pracownicy produkcji – 101 minut. Odpowiednio: 24% i 21% swojego czasu. To znaczy, że od ⅕ do ¼ czasu poświęcają na raportowanie, szukanie, wypełnianie, przekazywanie.
Wynika to, najczęściej, z błędów nie tylko w ułożeniu samych procesów, ale również – a może przede wszystkim – w ich czytelności i praktycznym funkcjonowaniu.
Pracownik traci czas na poszukiwanie narzędzi, gdyż nie ma standardów ich przechowywania i rozmieszczania. Oczekuje na komponenty, gdyż nie ma odpowiedniego systemu oznakowania i raportowania aktualnych stanów materiałów.
Przełożony przekazuje zmianę przez 38 minut, gdyż nie ma jasnego systemu raportowania, wizualizowania danych i aktualnych statusów. Poszukuje dokumentacji, gdyż nie ma odpowiedniego systemu składowania i obiegu dokumentów.
Czy można temu zaradzić? Oczywiście, że można!
Recepta
Oprócz samego ustawienia procesów, kluczowe jest ich odpowiednie zakomunikowanie i wizualizacja. Z pomocą przychodzi dobrze dobrane, przemyślane i dostosowane do potrzeb firmy oznakowanie.
- Tablice suchościeralne (wykorzystywane, np. jako tablice KanBan lub FIFO) pozwalają w czytelny i jasny dla wszystkich pracowników sposób zarządzać ludźmi i procesami. Ustawione w doskonale widocznym miejscu, stają się niejako centralnym punktem zarządzania produkcją. Informacje są jasne, klarowne, czytelne, przekazywane szybko i w zrozumiały dla wszystkich sposób. Tym samym pozwalają zaoszczędzić czas – pracownik i kierowników.
- Odpowiednie oznakowanie stanów minimalnych pozwala dostarczać komponenty na czas. Tablice cieni powodują, że pracownik ma wszystkie potrzebne narzędzia zawsze pod ręką. Tym samym – dłużej pozostaje na stanowisku pracy i nie marnotrawi czasu.
- Taśmy, naklejki, oznakowanie poziome, pionowe i wiszące – wszystkie te elementy pozwalają się lepiej zorientować w przestrzeni, a odpowiednie oznakowanie dróg i potencjalnych niebezpieczeństw nie tylko poprawia logistykę, ale też zmniejsza niebezpieczeństwo wypadków.
Pierwszy krok
Istnieje cała pula rozwiązań wizualnych, które wspomagają zarządzanie, zmniejszając marnotrawstwo czasu, zwiększając efektywność i podnosząc bezpieczeństwo. Kluczem jest odpowiednie zaprojektowanie całego systemu oznakowań oraz wdrożenie takich rozwiązań, które będą widoczne, intuicyjne i skuteczne w danym środowisku. Dlatego warto zacząć od audytu obecnych procesów i oznakowań, a później przystąpić do procesu zmian, które – starannie zaplanowane i przemyślane – wpłyną pozytywnie na efektywność całego przedsiębiorstwa.
Jako Tagatic od lat wspieramy firmy produkcyjne w tworzeniu bezpiecznych i skutecznych środowisk pracy. Umów się na bezpłatny audyt i dowiedz się, w jaki sposób możemy pomóc Twojej firmie.